Hongfeng VAC is an independent company in China, a professional manufacturer of high-tech PVD coating equipment for tools and multiple applications, as well as its components. We have been providing reliable quality PVD systems and our thoughtful services to clients from more than 20 countries all over the world for more than 10 years.
We promise to provide life-long service support for user equipment, including: equipment repair, maintenance, upgrade, transformation, relocation, spare parts, consumables, etc.
We promise to provide life-long service support for user equipment, including: equipment repair, maintenance, upgrade, transformation, relocation, spare parts, consumables, etc.
We promise to provide brand new, unused, safe and reliable PVD equipment, and meet the relevant national quality standards and laws.
YOUR APPLICATION
TOOLS, BLADES, MOLDS, DRILLS, HARDWARES
PLASTIC CAPS & DECORATIONS
CERAMIC TILES
GLASS & ACRYLIC MIRROR
PLASTIC CAPS & DECORATIONS
CERAMIC TILES
GLASS & ACRYLIC MIRROR
YOUR INDUSTRY
TOOL & HARDWARE MANUFACTURERS
MOLDS MAKER
COATING CENTERS
VACUUM METALLIZING FACTORY
MIRROR PLANT
MOLDS MAKER
COATING CENTERS
VACUUM METALLIZING FACTORY
MIRROR PLANT
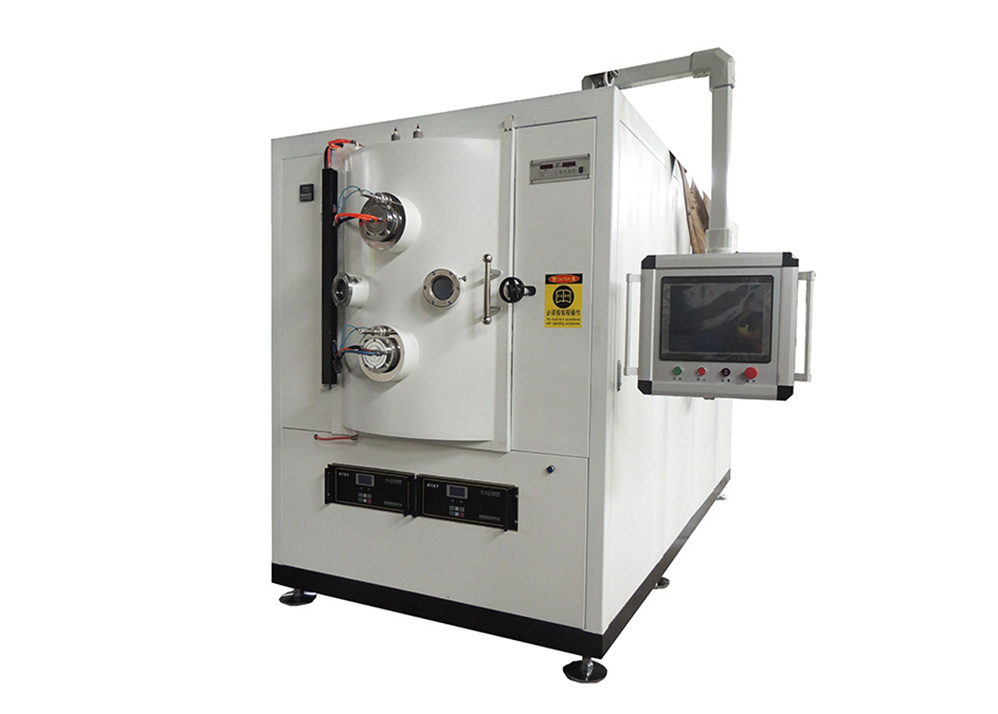
ARC-1000 Cathodic Arc Evaporation Machine
- 10~14 sets of cathodic arc evaportors for deposition
- Vacuum chamber volume [mm]: ø1000 x H1100
- Ideal size for industrial production
- Applications: Decorative and functial
- Diffusion pump/turbo molecular pumps options available
- Max. load: 500kg
- Optional: DC or MF magnetron sputtering system
- Footprint [mm]: L3200 x W1800 x H2300
Plasma Immersion Ion Implantation and Deposition System
-
Features* Stainless Steel double wall chamber with water cooling* Temperature control up to 350ºC* High voltage workpiece holder with water tower cooling and rotation* Filtered cathodic vacuum arc sources with full metallic plasma output* Kaufman ion sources for sample cleaning* RF-CCP source for gaseous plasma generation* High voltage pulse modulator for sample bias
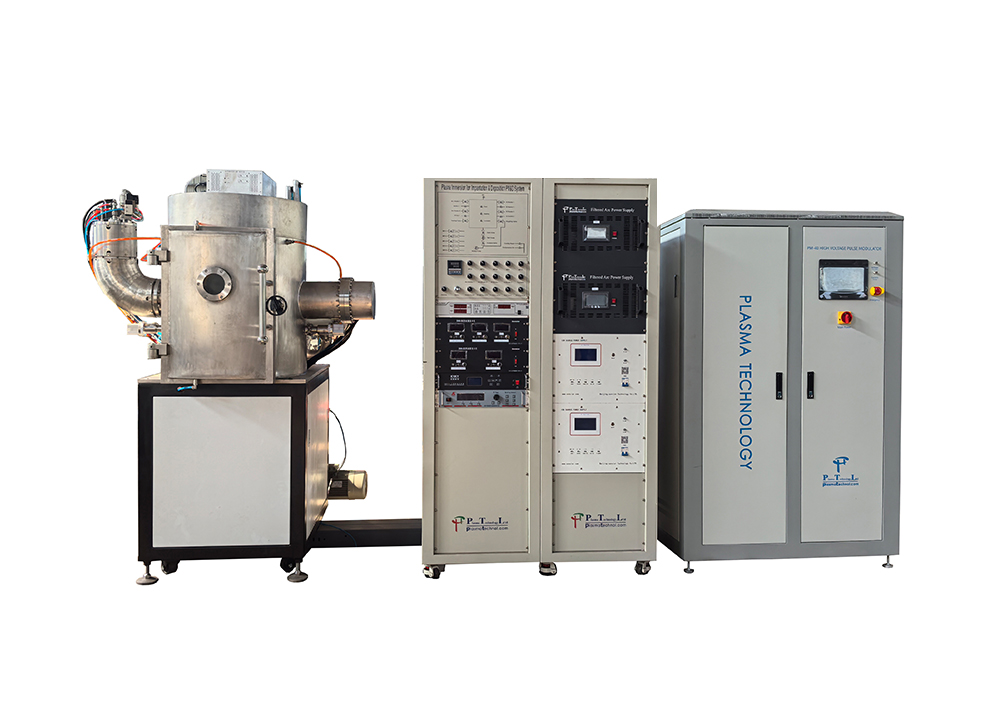
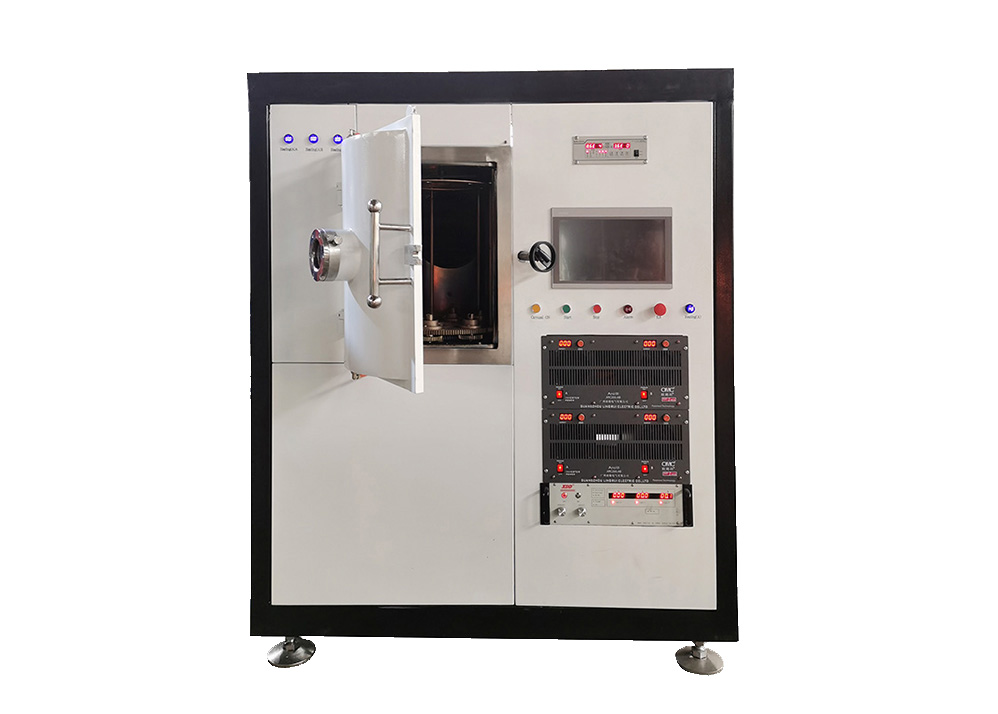
ARC-500 Small PVD Machine
- 4 sets of cathodic arc evaportors for deposition
- Vacuum chamber volume [mm]: ø500 x H600
- Smart option for small scale production
- Coatings: Decorative or functional titanium nitride(TiN), CrN, TiCN, AlTiN, etc
- Applications: Metal tools or stainless steel items
- Diffusion pump/turbo molecular pumps options available
- Max. load: 200kg
- Optional: DC or MF magnetron sputtering system
- Footprint [mm]: L2300 x W1500 x H1950
SP-1000 DC Magnetron Sputtering Machine
- DC or mid frequency magnetron sputtering cathodes
- Vacuum chamber volume [mm]: ø1000 x H1100
- Diffusion pump/turbo molecular pumps options available
- Type of magnetron: Planar or rotate magnetrons
- Application: Different metal coatings, optional composited coatings and multilayer coatings
- Optional: Cathodic arc evaporation system(AIP system). thickness monitor, linear ion source
- Footprint [mm]: L3200 x W1800 x H2200
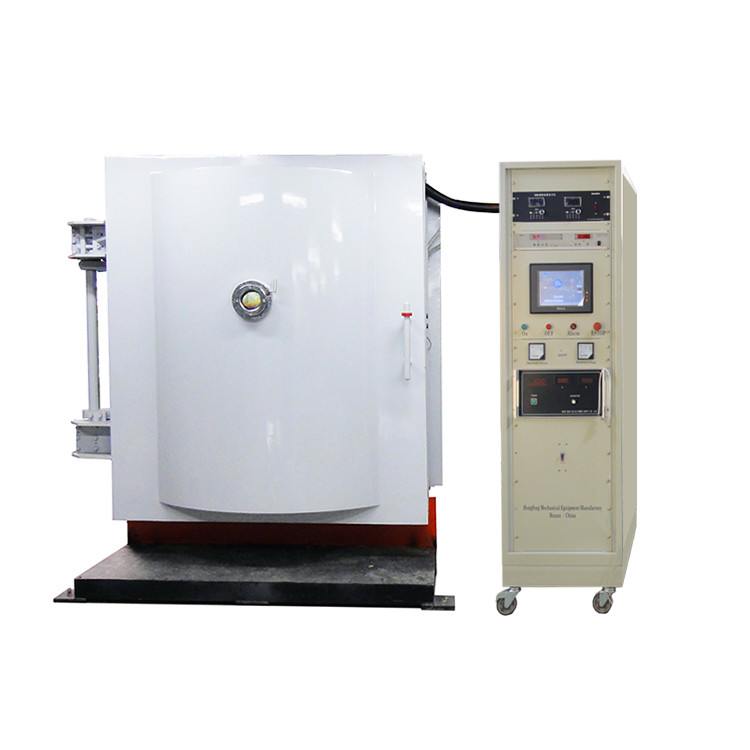
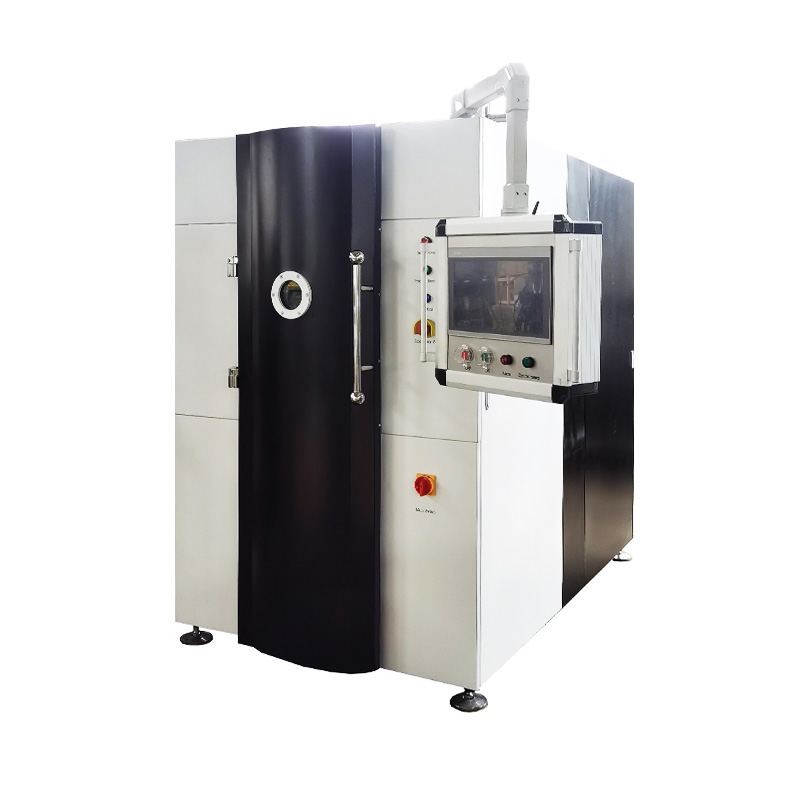
ARC-800 Arc Ion Plating Machine
- 6 sets of cathodic arc evaportors for deposition
- Vacuum chamber volume [mm]: ø850 x H900
- Coatings: Decorative or functional coatings
- Applications: Metal tools, molds, cutters or stainless steel items
- Diffusion pump/turbo molecular pumps options available
- Max. load: up to 450kg
- Optional: DC or MF magnetron sputtering system
- Footprint [mm]: L3300 x W1600 x H2200
EV-1600 Plastic Vacuum Metallizing Machine
- High efficiency thermal aluminum evaporation system
- Application: Apply metallic chrome coatings on plastic, glass, ceramic surface
- Raw material: High purity aluminum, tungsten wires
- Vertical or horizontal type of vacuum chamber
- One or two doors, or dual chambers model available
- Cycle time: 10-15 min.
- 4-6 batches/hour
- Footprint [mm]: L5000 x L2250 x H2300
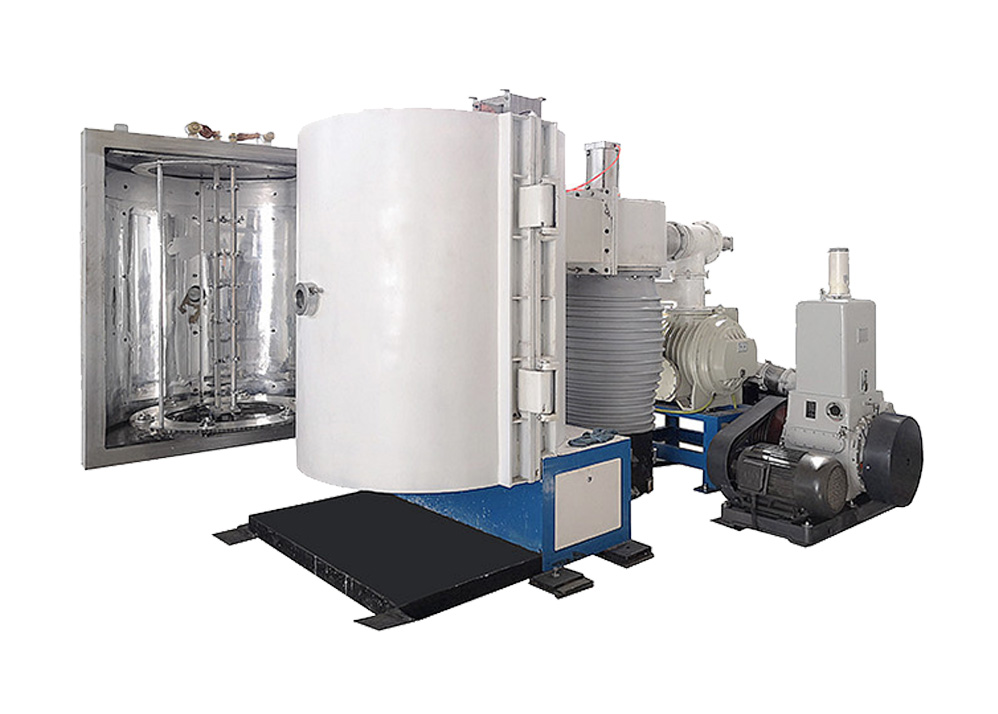
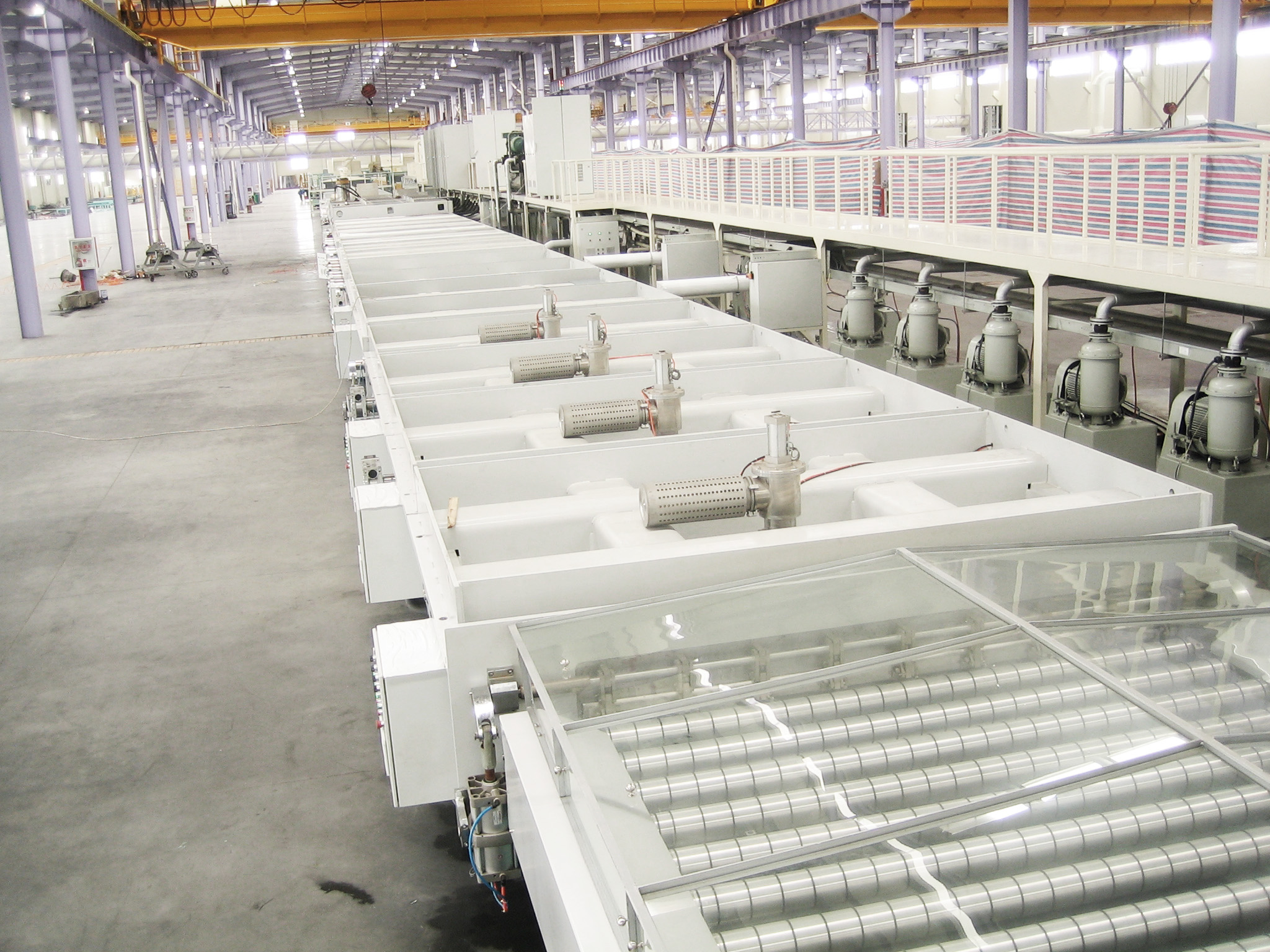
SP-3000 Glass Mirror Coating Line
- High efficiency magnetron sputtering systems
- Continuous inline sputtering coating
- Type of magnetrons: Rorate cylindrical DC magnetron sputtering
- Suitable for large scale production for aluminum or silver glass mirror
- Less labors needed
- 24 hours continue working
- Tact Time: 60-150 seconds
- Horizontal type, straight or curved line
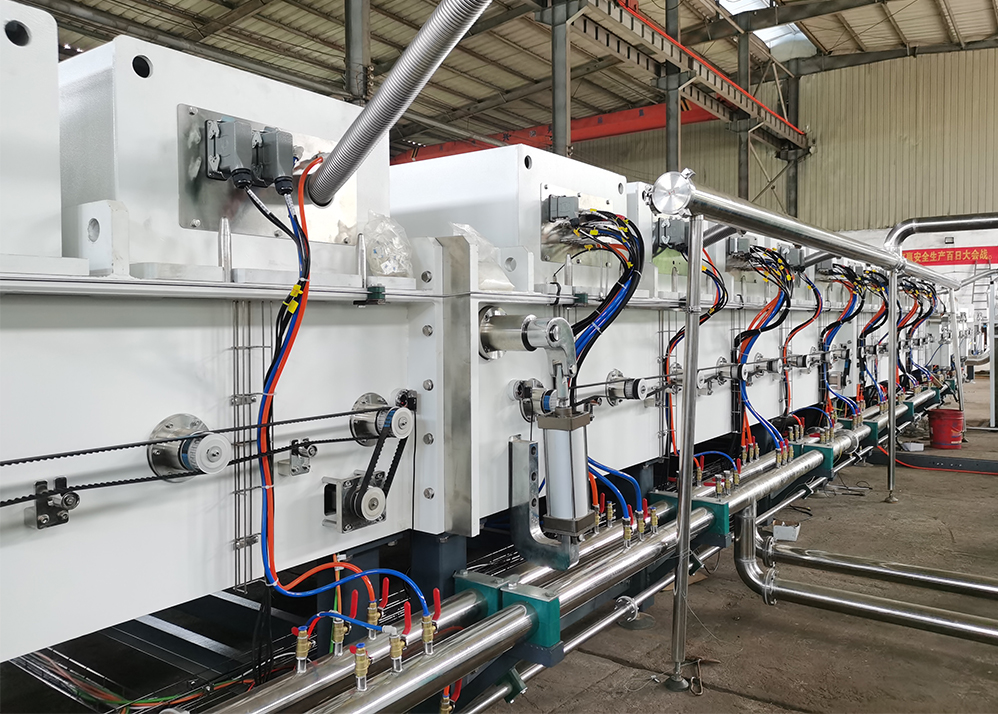
SP-5000 Inline Sputtering System for Antireflective Glass
- High efficiency magnetron sputtering systems
- Continuous inline sputtering
- Suitable for large scale production for antireflective(AR) glass
- Less labors needed
- High utilization of target materials with mid frequency cylindrical magnetron sputtering cathodes
- Horizontal type
- Ability for metallic, nitrides, oxides thin films deposition
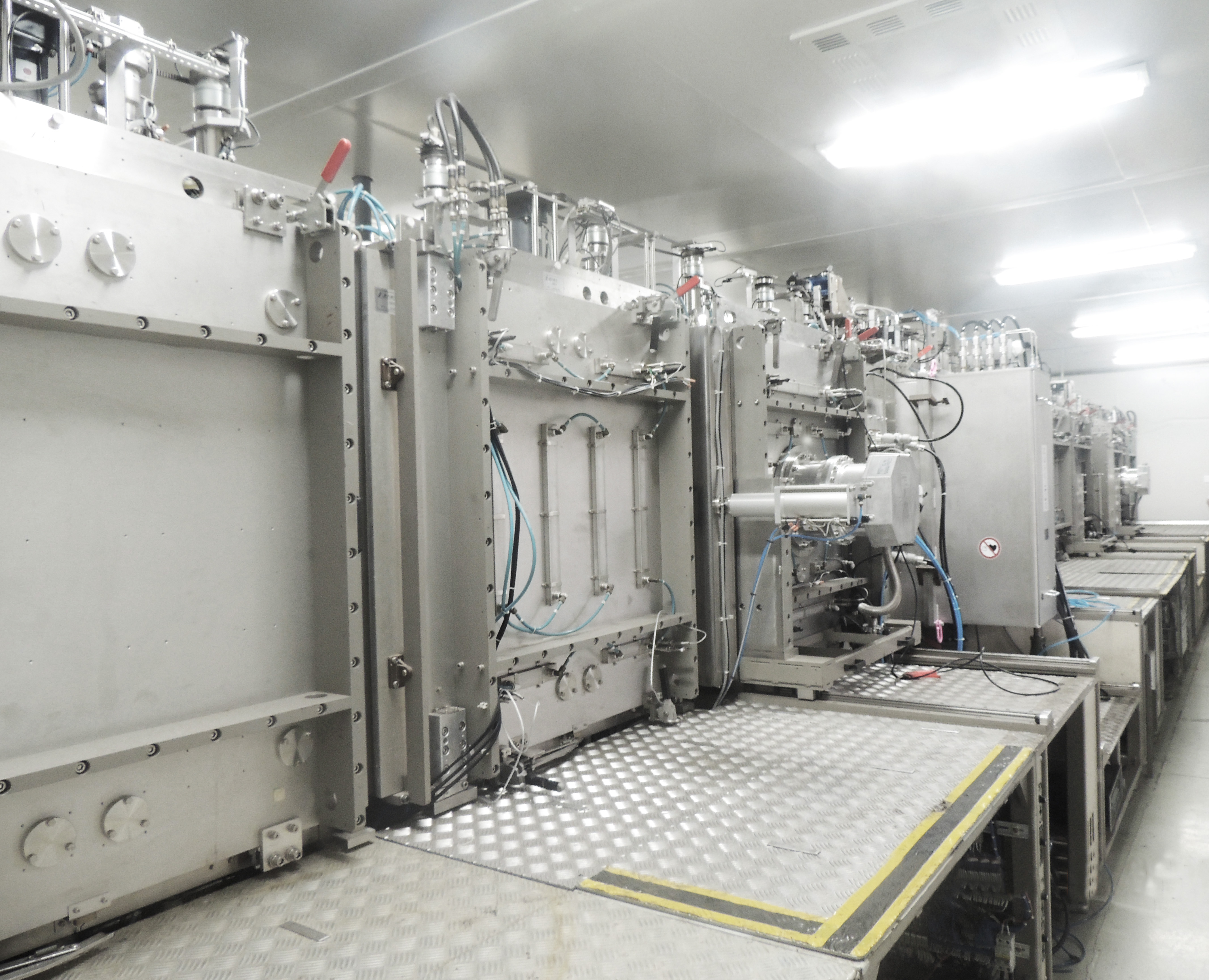
SP-8000 Inline Thin Film Deposition System
- Vertical Inline PVD equipment for continuous coating of flat parts (both sides simultaneously) using magnetron sputtering
- Suitable for large scale production for graphite bipolar plates(BPP)
- Stable quality of thin film coating layers
- High utilization of target materials with mid frequency rotating magnetrons
- Ability for metallic, nitride and oxide coatings as well as composite coatings